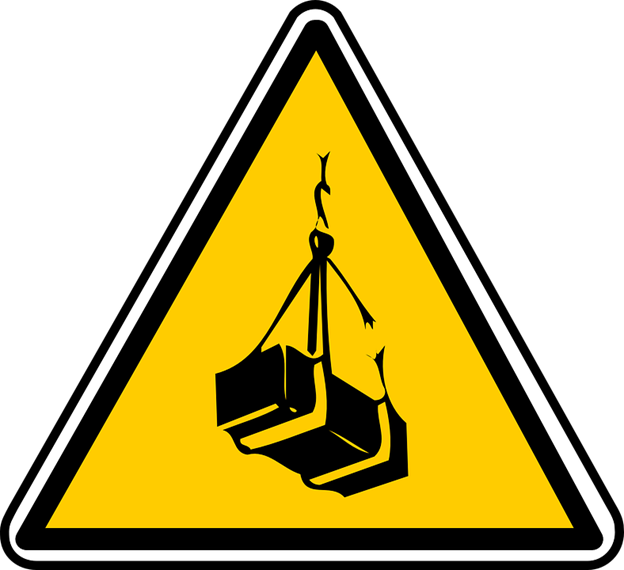
Ensuring Safety Above All: Best Practices for Rigging Inspections
Emery & Karrigan, Inc.
Safety is paramount in any lifting operation, and thorough rigging inspections play a crucial role in ensuring the well-being of everyone involved. By following best practices for rigging inspections, you can minimize risks, prevent accidents, and maintain a safe working environment. In this blog post, we will explore essential guidelines to help you conduct effective rigging inspections.
Pre-Use Inspection:
Before every use, conduct a comprehensive inspection of all rigging equipment. Carefully examine hooks, shackles, slings, and other components for signs of wear, damage, or corrosion. Ensure that each element is in proper working condition to guarantee the safety of the lifting operation.
Training & Competence:
To carry out rigging inspections effectively, personnel involved should receive proper training and possess the necessary competence. They should be well-versed in relevant regulations, industry standards, and safe rigging practices. Investing in training ensures that inspections are conducted by knowledgeable individuals.
Documentation:
Maintain accurate records of rigging inspections. Document the date, inspector's name, findings, and any actions taken. These records serve as a valuable resource for tracking maintenance history and ensuring compliance with safety regulations.
Inspection Frequency:
Establish a regular inspection schedule based on factors such as equipment usage, type, and environmental conditions. High-risk or critical equipment may require more frequent inspections. Consistency in inspections helps identify potential issues before they escalate into hazards.
Visual Inspection:
Perform a thorough visual examination of rigging equipment. Look for visible defects such as fraying, kinks, twists, or broken wires. Pay close attention to load-bearing areas and stress points. Identifying these issues early on allows for prompt repairs or replacements.
Load Testing:
Periodically conduct load tests on rigging equipment, especially after repairs or modifications. Adhere to industry standards and manufacturer recommendations for load testing procedures. This practice ensures that the equipment can withstand the intended loads without compromising safety.
Qualified Inspectors:
Assign rigging inspections to qualified individuals who possess the necessary knowledge and experience. Competent inspectors understand rigging equipment, its limitations, and relevant safety regulations. Their expertise ensures accurate assessments and reduces the risk of oversight.
Replacement Criteria:
Establish clear criteria for determining when rigging equipment needs to be replaced. Factors such as wear, damage, or exceeding safe usage limits should be considered. Having well-defined guidelines helps make informed decisions regarding equipment replacement and ensures continued safety.
Communication & Reporting:
Foster a culture of open communication regarding rigging equipment. Encourage employees to report any observed issues or potential hazards promptly. Establish effective communication channels to ensure that concerns are addressed in a timely manner, fostering a proactive approach to safety.
Conclusion:
Maintaining a safe working environment is a shared responsibility, and adhering to best practices for rigging inspections is a crucial step in achieving this goal. By conducting pre-use inspections, providing adequate training, documenting inspections, and following visual inspection, load testing, and replacement criteria, you can enhance safety and prevent accidents. Remember, safety should always be the top priority in every lifting operation.
Take the initiative to implement these best practices and share this information with your colleagues and peers. Together, let's prioritize safety and ensure that rigging inspections are conducted with the utmost care and attention.